Bank of Ireland head of Manufacturing Sector Conor Magee reveals defence strategies for SMEs battling to overcome the current global supply chain headache.
2021 will be remembered as the year of the supply chain tsunami where previously trusted global supply models were exposed for their fragility and became focus of C-suite leadership attention across the globe.
A combination of Covid-19, Brexit, high demand, transport interruptions and climate change weather events, have all conspired to a perfect storm of disruption for manufacturing not witnessed since the invention of the humble shipping container back in 1956 which was instrumental in kick-starting global supply chains.
“The inter-dependency across different manufacturing sectors has been highlighted and destabilised like never before”
Manufacturing has gone from lean to a lot less lean, from just in time to just in case, from certain lead times to uncertainty, from stable prices to double digit inflation, from labour supply to labour shortages and from road and sea transport to expensive air freight.
The eye of the storm is everywhere
The inter-dependency across different manufacturing sectors has been highlighted and destabilised like never before. Perhaps the best example of this is the automotive and semiconductor sectors.
Semiconductor availability or chips shortage has been severely impacted by a combination of demand spikes during Covid (chips diverted to gaming, data centres, laptops, TVs), weather events (Texas, Taiwan) and new Covid surges heavily impacting chip making geographies (Japan, Malaysia)
Even though available supply has been increasingly diverted to the automotive space, because of latent high demand, supply is still well behind required volumes and so car plants are in idle mode, short working or operating what’s known as a “build shy model.”
Cars need anything from 700 -1000 chips to accommodate the ever growing kaleidoscope of features that car brands offer. So how does the “build shy model” work? Well automakers have been forced to drop features to use less of available chips per car. Features like blind spot alerts, fuel consumption and lumbar support are for now not always available. It has become a reputational balancing act between long delivery times or shorter times with less features. Furthermore they are focusing on higher volume brands for chip allocation to maximise revenues.
In more extreme “build shy” cases where other components are in short or late supply, car makers have been forced to fill parking lots with unfinished cars to keep factories running, precious labour engaged and then turnaround cars quickly to customers when the missing components arrive.
Similar tactics are been adopted by Irish SMEs with latest PMI data showing a combination of high level of unfinished goods and low levels of finished goods.
Estimates of losses for global car maker are at levels of €100bn in this year. Supply chain pain disruption estimates globally stand at in excess of €4tn
In the medium to long term manufacturers will be forced to reconfigure and take greater control over their supply chains to guarantee resilience.
If we step back from this sector example and helicopter view the global issues to think about strategies for defence. First let visualise the problem. When I think of supply chain structures and that the strength of the links and building blocks are the most important, two images come to mind. First the game of Jenga and second the famous “Jenga” clip in the movie The Big Short. This clip, with great impact, characterises the US housing market with a tower built on cheap and reckless credit. Even if you have already seen the movie, take a moment to watch the clip and imagine that the wooden blocks represent shipping containers containing critical components. Consider the model below.
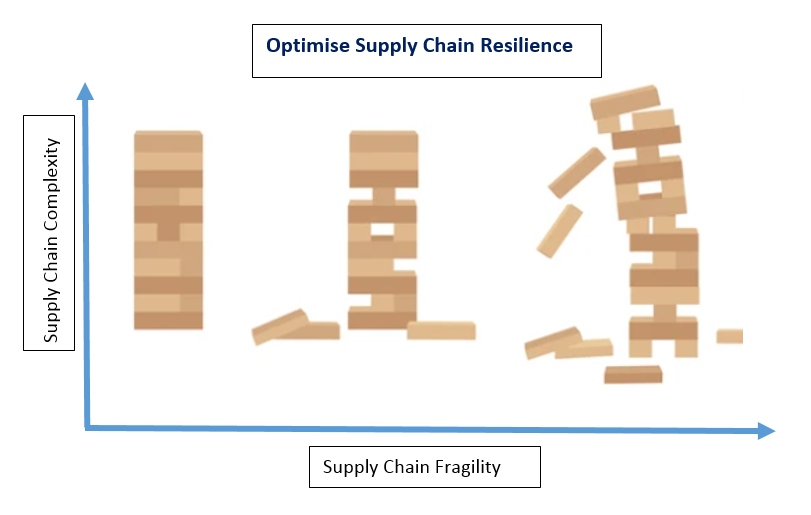
On the left is a robust and resilient supply chain, the aim of every manufacturing entity. The right amount of suppliers, a manageable level of complexity, and a solid supply and logistics infrastructure. In the middle is what all manufacturing experiences from time to time, namely some component shortages and supply chain disruption but we manage to keep the structure in place and mitigate the lost/late parts with say air freight. On the right we are in tsunami territory, multiple parts and containers fall simultaneously out of the supply chain, the usual mitigation measures are not adequate, the trusted just in time supply chain structure collapses and we have to reconfigure from scratch.
Mindset model
So how can manufacturing move to the left hand side above. Well one thing manufacturing is all about is problem solving and manufacturers typically employ a range of structured problem techniques such as 5 Whys, fishbone diagrams, scenario planning. However recent events require techniques with more creativity, mindset changes, which challenge the status quo and motivate transformational change. With this in mind a good place to start is with the mindset model shown below.
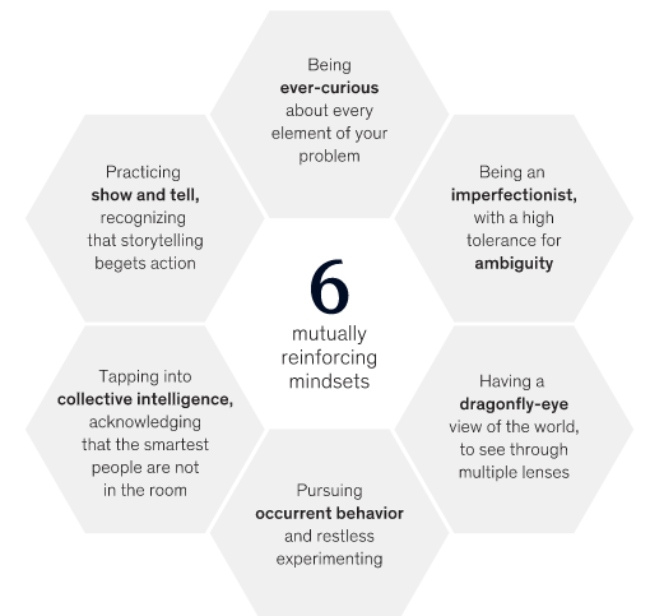
If we aligned these problem solving mindsets and behaviours to the supply chain, SMEs may discover and in many cases have already implemented following changes:
Ever curious: Behave as you did when you were 4 years old, don’t be handcuffed by norms developed with age and ask relentlessly why we are doing things the way we do them now. Why are we shipping parts half way across the world with delivery uncertainty when a local solution is available? Many Irish SMEs have insourced processes which were previously considered non-core
- Imperfection & Ambiguity: Perfection is the enemy of good enough. Embrace trial and error rather than rushing to a rigid end solution. Experiment with new suppliers who were previously discounted because of price. Perhaps their greener solution wins out in the long run
- Dragonfly View: Like a dragonfly with a complex eye structure, see the problem and solutions through multiple lenses. Many Supply Problems are being solved with increased adoption of digital tools, such as real time data driven ERP systems or technologies such as 3D printing to reduce components. In turn many of the solutions solve other problems as in near shoring reduces carbon footprint.
- Pursue Occurrent Behaviours: This is what actually happens at a place in time and not what might happen. Supply chain problems are complex, so it is important to understand with data what is actually happening to separate and solve the interwoven complexities. JIT models were designed with a seamless uninterrupted logistics model in mind with precise reorder quantities. Manufacturers are breaking away from that hypotheses by going less lean, critical component stock building and a more JIC (just in case) mindset to safeguard their reputations with loyal customers
- Collective Team Intelligence: Adopt flatter organisation structures and allow everyone a voice in addressing the problem. The smartest people are not the leadership team. Fortunately Irish manufacturing benefits from enormous talents and skillsets. Creative problem solving, agile decision making and leadership with empathy have all been stepped up in spades as both MNCs and SMEs continue to successfully navigate supply headwinds. Great optimism abounds across manufacturing with latest November BOI Pulse and AIB PMI data signalling further strong growth into 2022 and a sense of chinks of light at the end of supply chain tsunami tunnel. More on this in a moment.
- Show and tell: Going back to being curious. As a parent of a curious 4 your old you use their great questions to show and tell what the answers might be. You connect with them at their level and ensure they are inspired to action. The same applies to big people problems including supply chain. It is imperative to get people on-board with the solutions by making the solution real and tangible. Demystify the problem and solution which at first inception may have appeared complex and unworkable. Digitalisation related to supply chain is a good example here. Very often SMEs are not capturing available data to their advantage and some data analysis insights can show and tell hidden and often with hindsight easy solutions.
Chinks of light and Green Shoots of Improvement on horizon for 2022
Looking ahead to 2022, both the latest BOI Pulse data and AIB PMI data are suggesting a lesser amount of supply disruption in November compared with October plus investment plans for capacity increases are both good news signals for Irish Manufacturing.
On the global stage and another chink of light is that the Baltic Dry Index (BADI) which measures cost of maritime transport is starting to fall.
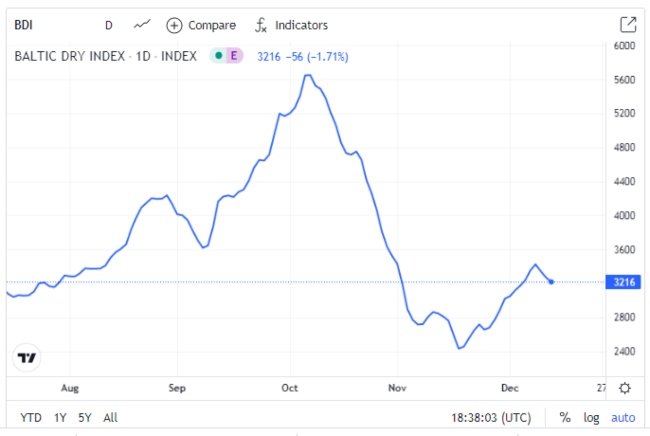
BADI was below 500 pre pandemic, has risen to 5497 in October and recently dropped back to 3272. This combined with less congestion in china ports plus evidence that forward priced shipping contracts are lower suggest that shipping costs and delays will ease in 2022.
Other factors are at play such as seasonal demand factors which will fade in Q1 2022 again swinging the supply chain mood upwards.
In summary this writer believes that after a year like no other Manufacturing can now deservedly look forward to Happy and Restful Christmas Break followed by renewed optimism for 2022 grounded in the belief of a sharper equilibrium between supply and demand.
Merry Christmas and A Happy New Supply Chain 2022!