Machine Eye Technology have pioneered cutting edge automation to augment heavy machinery and farm safety. Founder, Brendan Digney provides a glimpse under the hood of this ground-breaking and prescient technology.
On a farm tractor where do you locate your sensor technology?
A farm tractor is something many of us can picture and, in some way, are familiar with. When we install our system, we don’t actually change the appearance of the tractor. All we do is replace the existing external stock mounted work lights; located at a high level, at the roof-line corners, to the rear of the tractor cab; with our own high-powered LED package. These packages also contain an artificial intelligent backed sensor which enables the system to provide and to optimise for safety. Essentially, we remove the existing lights and put our own sensor equipped work lights on instead, finally fitting a control system, installed beneath panels within the tractor cab itself.
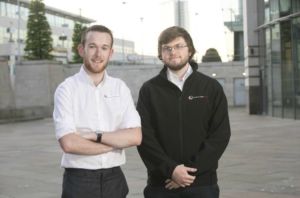
How can Machine Eye improve farm safety?
It’s important to note, that since 2009, thirty percent of all farm fatalities are machinery related. A farm machine travelling down the road at 40kmph certainly has potential to cause you harm. However, the greater proportion of farm machinery accidents occur when farm machinery is either idling or moving slowly within the farmyard, where people are generally at a higher risk of accidental injury. Essentially the use case, is where there is close personal contact, allowing Machine Eye to monitor your position and behaviour, while working in the vicinity of the machine. In a scenario where you have a person moving unsupervised into a yard, we’re already seeing really positive results. We are detecting them, and we are tracking them. We are also tracking multiple persons within the proximity of the machine and that is significant; and it’s all very much down to the state-of-the-art artificial intelligence that we have developed.
A key factor has been the exponential rate in the evolution of technology. The cutting-edge hardware we now deploy has permitted us to move at speed; and achieve something we couldn’t have achieved just two years. It has allowed us to do ‘edge processing’, which enables intense computational work, all without the need to have massive servers or to be connected. This means that we can put a highly customized processor into a device out in the field, and it can do this in real-time. We are now deep into R&D because with a safety device you don’t want to rush it to market. You want to be 100 per cent sure of what you’re delivering for your customers and 100 per cent sure of that system. We continue to fine tune our algorithms for performance in field trials, performing longer term testing, allowing the algorithms to learn and refine.
“The greater proportion of farm machinery accidents occur when farm machinery is either idling or moving slowly within the farmyard, where people are generally at a higher risk of accidental injury.”
What are the main types of farmyard accidents involving machines?
There are a couple of key areas and a primary focus and concern being the power take-off (PTO) shaft. Many in farming are aware of the danger of becoming entangled in a tractor’s PTO shaft or even a faulty PTO shaft cover; and this is something very much at the core of what we do. When a machine is static and the PTO is rolling; our system watches like a hawk, ready to act in an instant which is key to our safety system. A lot of accidents also occur due to collision. During silage-making there are a lot of machines about, moving forward, moving back, involving a lot of repetitive actions. Repetition causes mistakes and repetition is where accidents can start to occur, particularly over an eight or nine-hour working day, when filling a silage pit or clamp. However, a key aspect about electronics and digital systems is that they don’t get tired and are always alert, providing automatic safety. However, it’s not a replacement for acting responsibly or acting safely as the system helps augment the machine operator’s own situational awareness, not replace it.
What assistance have you received on your start-up journey?
While completing a masters engineering degree in Queen’s University Belfast, we initially received help from the university before being accepted on an ‘Ireland Funds Business Plan’ programme with the NDRC in Dublin. The course was transformative with a key emphasis on lean business modelling and customer validation. We also received great support from the ‘Invent Programme’, sponsored by Bank of Ireland, through Catalyst Inc, based in Belfast; then with Santander Bank and their university entrepreneurship programme and finally, with Enterprise Ireland’s innovation arena at the Ploughing Championships.
“When a machine is static and the PTO is rolling; our system watches like a hawk, ready to act in an instant which is key to our safety system.”
How is your technology different to what’s already on the market?
At the minute, there is nothing quite like our offering. Two years ago, the enabling technology for this kind of system wasn’t available, whereas now it is. However, I am not going to say that it’s an off-the-shelf type technology, but it is quite accessible. Our secret sauce is really the innovation and the core technology that has been in developed over the last number of years, across the universities and across the island – and we were fortunate to be able to access that.
Your ambition?
I can foresee the potential for this technology, and not just in agriculture. There is a real need for this technology, right across the board, under its various iterations and guises. It has the genuine capability to make a real impact on people’s lives by preventing accidents and making a difference. That’s the ambition and we just need to keep the head down and continue working towards that goal.
Interview by Brendan Byrne